Efficiency and flexibility are important parts of a good production process. Odoo, an open-source ERP software, has been in the forefront of providing businesses with powerful tools for managing their operations effectively.
With the release of Odoo 17, the Multi Bill of Materials (BOM) features adds a new layer of complexity to manufacturing processes.
This blog looks at Multi BOM production in Odoo 17, including its importance, setup, and benefits. Generally, a Bill of Materials (BOM) is a thorough description of the components, assemblies, and raw materials needed to manufacture a product.
However, in real-world production circumstances, items may have variations or alternatives that need distinct sets of components. This is when the Multi BOM feature comes into play.
Multi BoM allows organizations to define numerous BoMs for a single product, each representing a specific variation or choice. These changes could include variances in size, color, material, or any other adjustable feature.
Manufacturers gain flexibility by correlating distinct BoMs with product variants, allowing them to adapt their manufacturing processes to diverse consumer needs.
Let's use an example to demonstrate how to manage several Bills of Materials in the Odoo 17 Manufacturing module.
Assume that the corporation wishes to produce a table. A table contains several components, including a tabletop, legs, screws, and so on.
The tabletop has a variety of components, including wooden panels. Two bills of materials (BOMs) are required to meet the production requirements: one for the table and one for the tabletop.
The table BOM contains components such as the tabletop, table legs, screws, and bolts.
Meanwhile, the tabletop BOM should be set up to generate as many tabletops as necessary for the tables being produced.
Routes must be established in three ways: manufacturing, MTO (make-to-order), and buy. The Manufacturing route is used for products that need to be produced at the source location, and a manufacturing order is issued to meet demand.
The MTO route ignores available stock, instead generating an RFQ or draft Manufacturing Order regardless of inventory levels.
The Buy route is used to meet product criteria at the destination location, resulting in a request for a quote.
By establishing these routes and BOMs, the production and procurement operations may more effectively respond to demand fluctuations.
Let us enable routes for each of the table components. The tabletop routes should include both MTO and Manufacturing.
The routes for the table legs must be configured to MTO and Buy. This combination enables the quick preparation of RFQs when the product is unavailable, ensuring timely purchase when necessary.
The bolt and screw paths have been set to Buy, similar to how the table legs were configured.
The surface, table leg, screw, and bolt are required to construct the table's first bill of materials (BOM). The components for the second BOM, assigned for the tabletop, are wood panels.
Another bill of materials for the manufacturing process is contained within the wood panel, resulting in a multi-level bill of materials structure.
When the manufacturing order for the 'table' product is approved, a child manufacturing order is automatically generated.
After you've established the necessary raw materials, go to the Product menu and select the option to create a bill of materials (BOM).
You should prepare two bills of materials:
1. Tabletop:
Components: Wood panel.
Description: The wood panel's bill of materials includes a ply layer and a wear layer.
2. Table
Components : include the tabletop, legs, screws, and bolts.
Description: This bill of materials lists all of the components needed to assemble the table.
Navigate to the Bill of Material for the tabletop. It includes the component known as the Wood panel.
The Wood panel has an internal bill of materials that includes the Ply Layer and Wear Layer components.
This displays the ability to generate several bills of materials inside a hierarchical system. The Ply Layer and Wear Layer are the matching components of the Wood panel, and the BOM type is set to manufacture the product.
Manufacturing operations are listed on the "Operations" tab. To incorporate additional actions, click "Add a Line".
When adding operations, be sure to indicate the work center and the default time required to process the order.
Similarly, for table production, the operation type is provided to outline the necessary phases in the manufacturing process.
Now, let's make a manufacturing order for the product Table.
You must enter the product and quantity to be produced, as well as pick the proper bill of materials.
Once the bill of materials is uploaded, the components are automatically populated depending on the information supplied in the BOM.
The "Work Order" tab contains extensive information about the operations, such as the designated work center where each operation will take place, the projected duration of each operation, and other essential details.
Following order confirmation, you will see the production of two purchase orders for raw materials: screws, bolts, and table legs. In addition, a child manufacturing order (MO) is created to produce the tabletop.
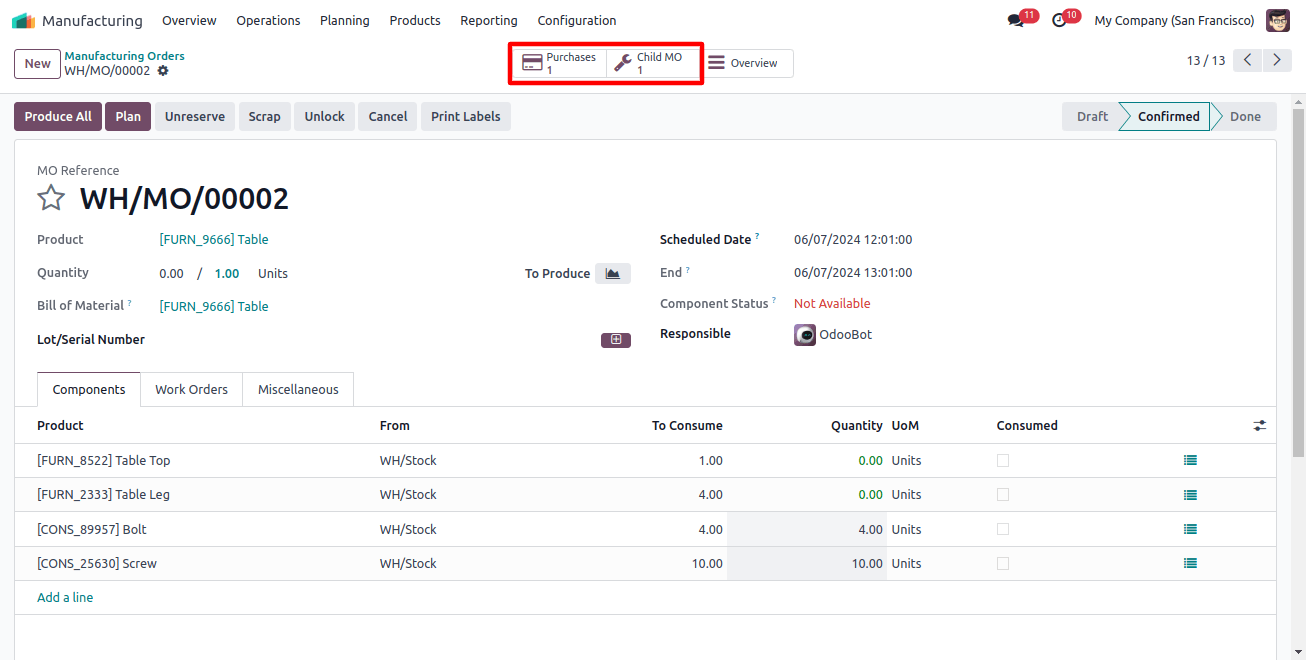
Upon analysis of the created MOs, you will discover another child MO for producing the wood panel within the tabletop MO.
This demonstrates the capabilities of a multi-level bill of materials. It is critical to complete the fabrication of the child MO before the tabletop can be consumed to ensure a smooth progression of product production.
Access the three purchase orders, confirm them, and then receive the merchandise.
Once the purchases are completed, the product consumed will be instantly updated to reflect the relevant quantity.
Now go to the child manufacturing order (MO). After confirming the production order for the product table, the first stage is to produce the tabletop.
However, before the tabletop can be manufactured, the wood panel must be finalized.
After accessing the Tabletop MO, it is critical to confirm the availability of the required components and proceed with the manufacturing process accordingly.
After finishing the production processes for both the tabletop and the wood panel, you will notice that the MO for the table moves to the "ready" status.
Since the creation of the child MOs has been completed, you may now proceed with the finalization of the table's production.
In the "Work Order" page, begin the manufacturing process by starting the operation and progressing through each stage until finished. Once all activities have been completed, click the "Done" button to mark the work order as completed.
Throughout the process, bills of materials for the tabletop and table were created, operations were configured, raw material purchases were made, child manufacturing orders were managed, and after completing the manufacturing steps and marking the work order as done, the final product, the "Table," was ready for delivery to the customer.
The Multi Bill of Materials functionality in Odoo 17 transforms manufacturing operations by providing unprecedented flexibility, efficiency, and precision.
Businesses that smoothly integrate Multi BoM capabilities into their workflows can react to changing client expectations, streamline production processes, and gain a competitive advantage in the market.
Finally, learning Multi BOM in Odoo 17 Manufacturing offers considerable benefits for optimizing production processes and increasing operational efficiency.Multi BOM enables firms to better manage complicated manufacturing requirements and allocate resources. Using Odoo Services can help you optimize this installation, providing seamless integration and the full benefit of Odoo 17's sophisticated manufacturing capabilities.
Related Post:
- What Are the Steps to Implement Multi-BOMs in Odoo 16 Manufacturing
- Master Odoo 17 Manufacturing with Bills of Materials
- How To Make Manufacturing Order From A Sales Order In Odoo
- How Do Product Variants Work in Odoo 17 Manufacturing
- What Are The Best Practices For Managing Manufacturing Lead Times in Odoo 17